Managing inventory can be tricky, but with the right approach, you can avoid common mistakes that many businesses make. In this guide, we’ll walk you through some of the most frequent inventory management pitfalls and show you how to steer clear of them using Tracmor.
1. Inaccurate Inventory Counts
The Mistake:
One of the most serious issues in inventory management is having incorrect inventory counts. This may end up in stockouts, overstocking, and, eventually, reduced profits or wasted resources.
How to Avoid It:
Tracmor makes it simple to maintain correct inventory counts by updating your data on regularly. Use the barcode scanning tool to quickly and accurately track products as they enter and exit. Schedule regular inventory checks with Tracmor’s reporting tools to ensure that everything matches.
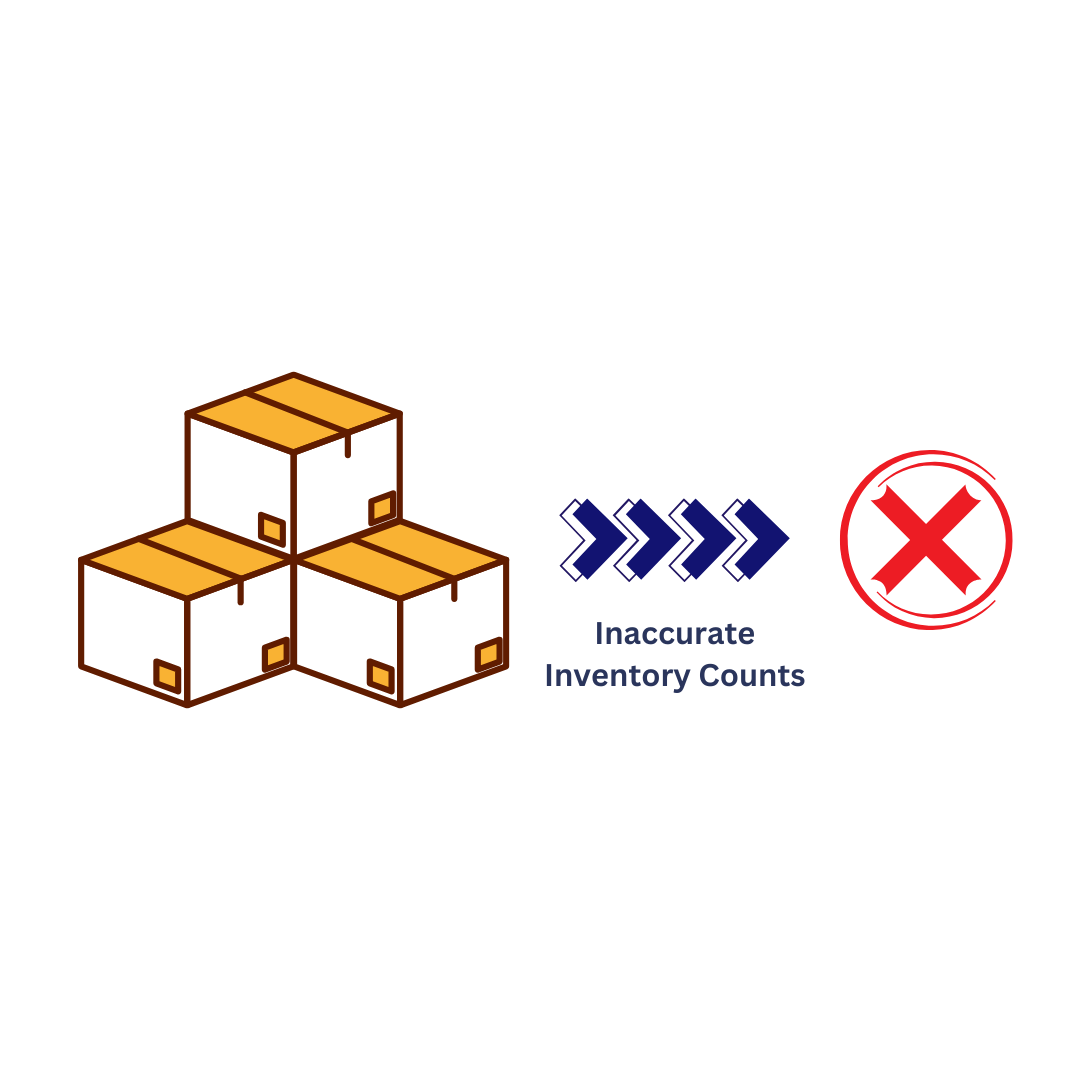
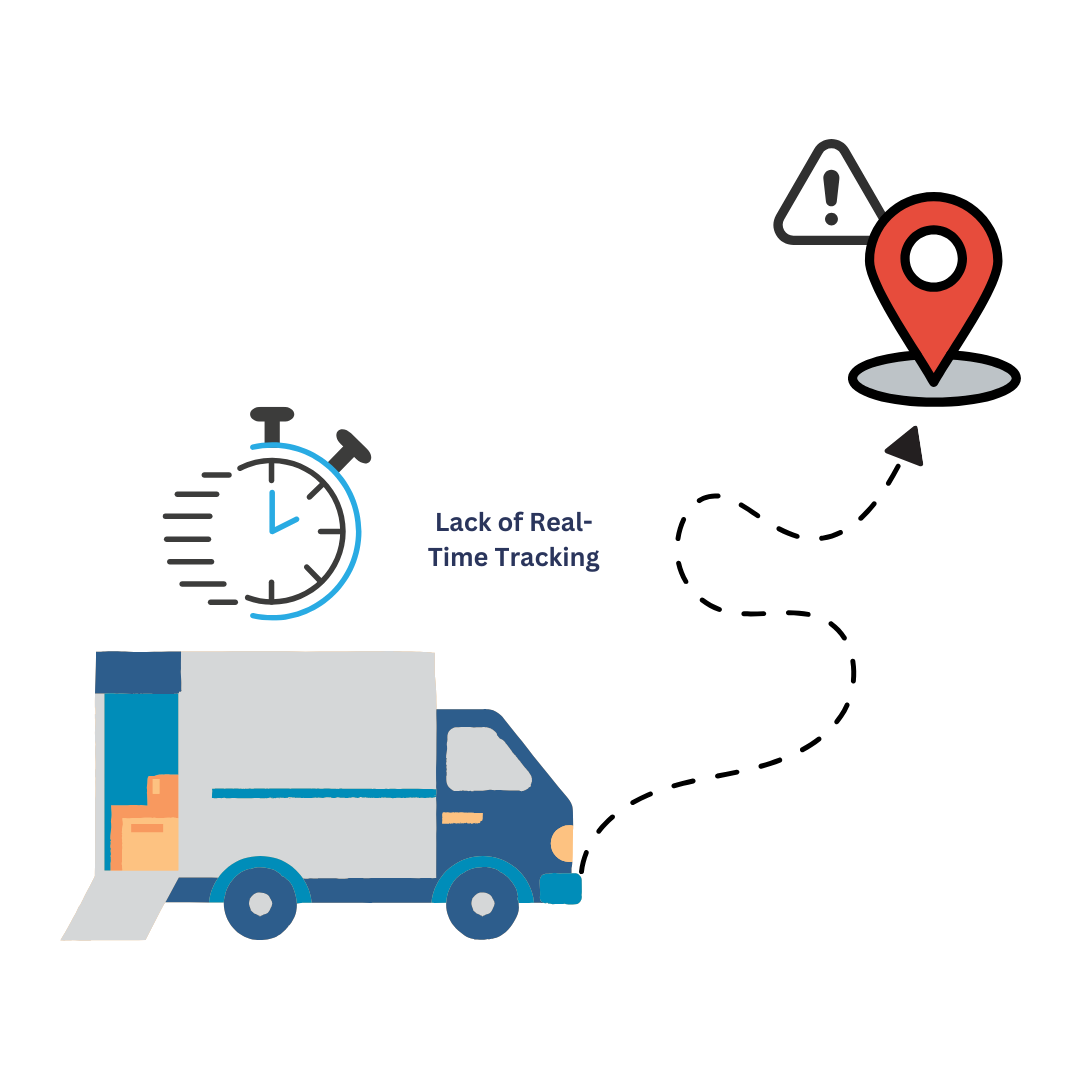
2. Lack of Real-Time Tracking
The Mistake:
Not having up-to-date inventory tracking can lead to delays in restocking, missed sales opportunities, and difficulties in managing demand effectively.
How to Avoid It:
Tracmor makes it simple to maintain correct inventory counts by updating your data on regularly. Use the barcode scanning tool to quickly and accurately track products as they enter and exit. Schedule regular inventory checks with Tracmor’s reporting tools to ensure that everything matches.
3. Manual Data Entry Errors
The Mistake:
Entering data manually can lead to mistakes, like typos or missed entries, which create inaccurate inventory records.
How to Avoid It:
Tracmor’s barcode scanning feature helps reduce errors by letting you scan items directly into the system. This way, your records stay accurate without relying on manual entry.
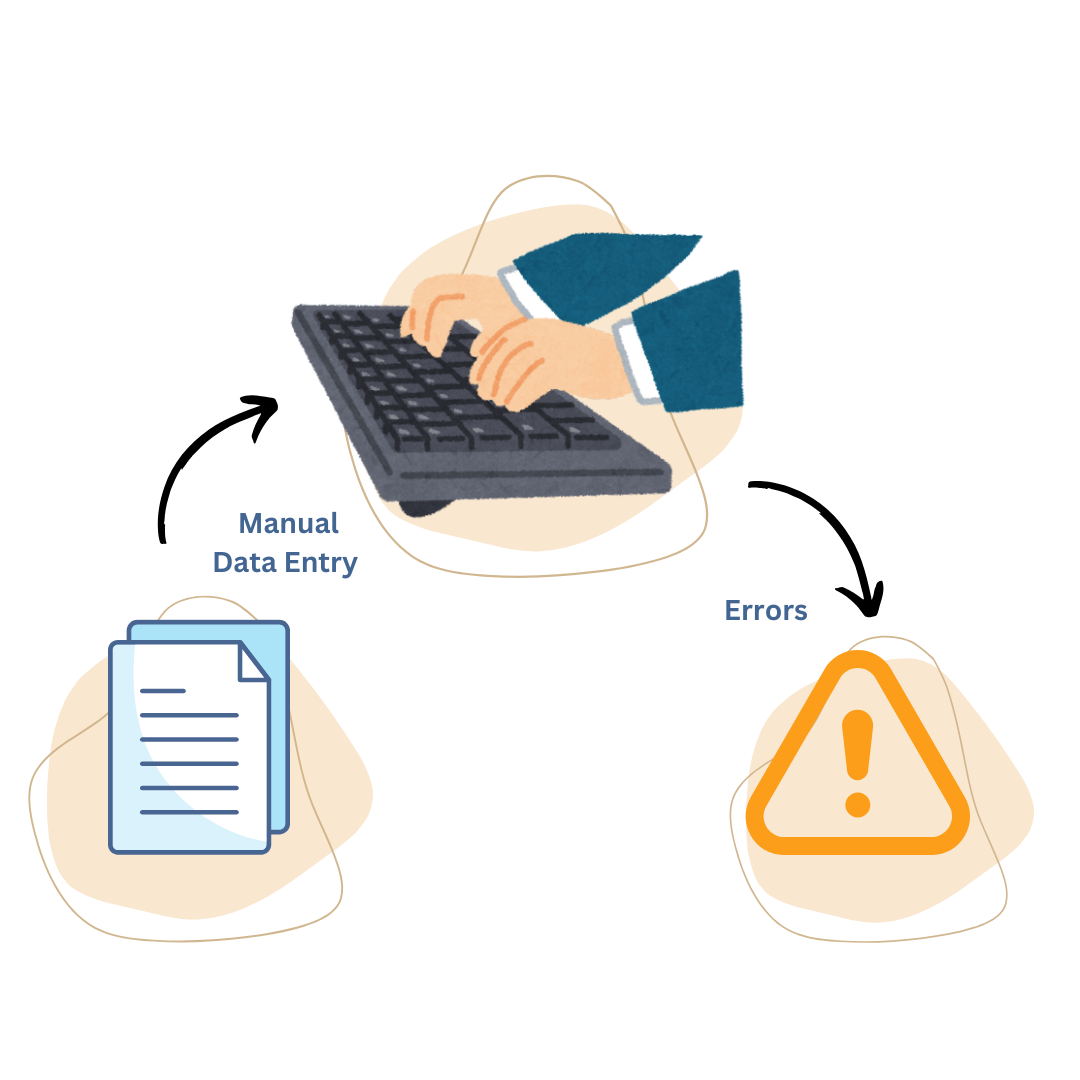
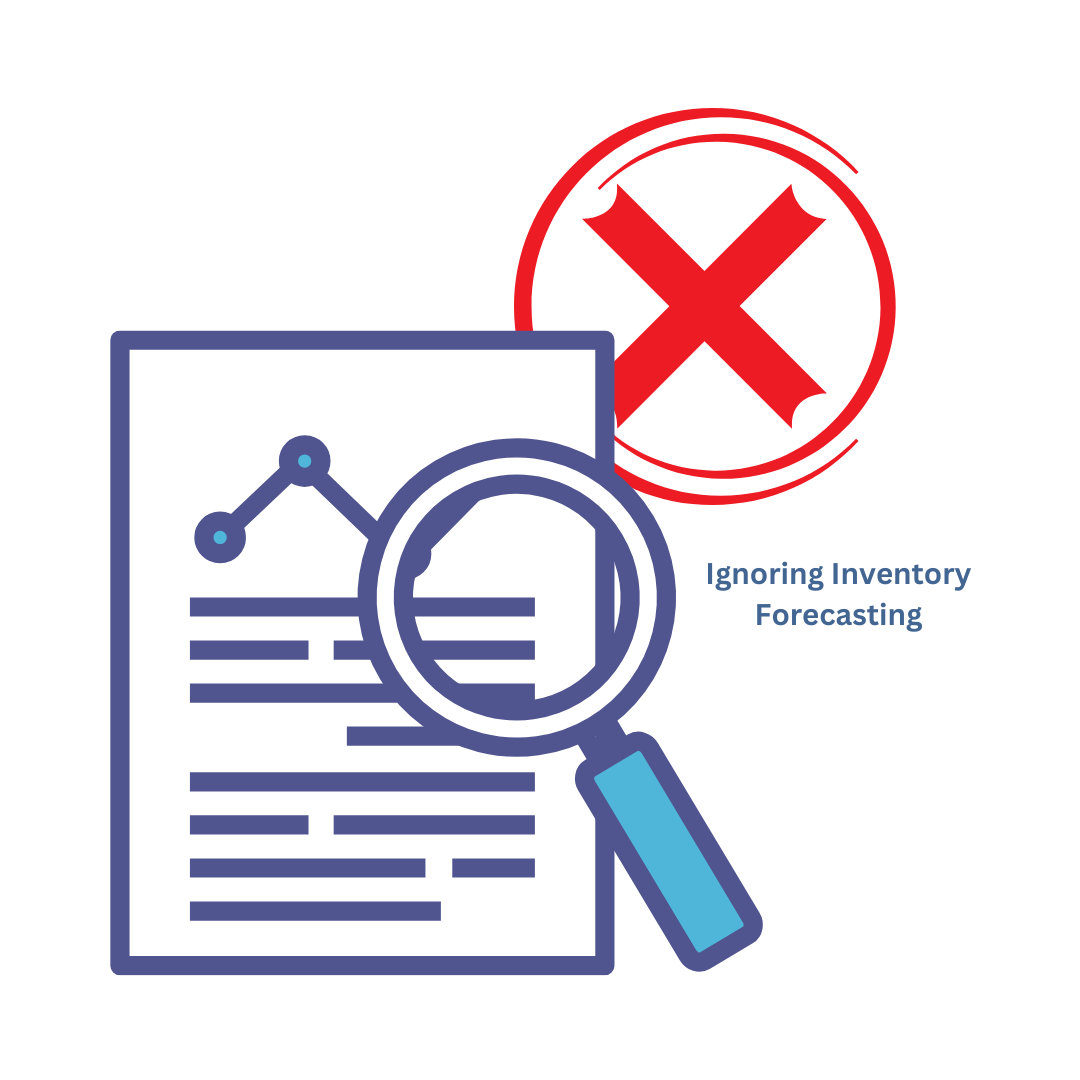
4. Ignoring Inventory Forecasting
The Mistake:
Overstocking or stockouts can occur from failing to calculate inventory requirements, both of which can be damaging to your company’s operations.
How to Avoid It:
To predict your inventory demands, use Tracmor’s reporting tools. In order to stock the right amount of inventory at the correct time, you need to examine past sales data and trends to predict future demand.
5. Poor Organization of Inventory
The Mistake:
An unorganized inventory can lead you to lose time and make it harder to find goods when you need them, which can cause your business to run more slowly.
How to Avoid It:
You can organize and categorize your inventory with Tracmor to make it simple to find. The asset tracking features of Tracmor can assist you in keeping your system organized.

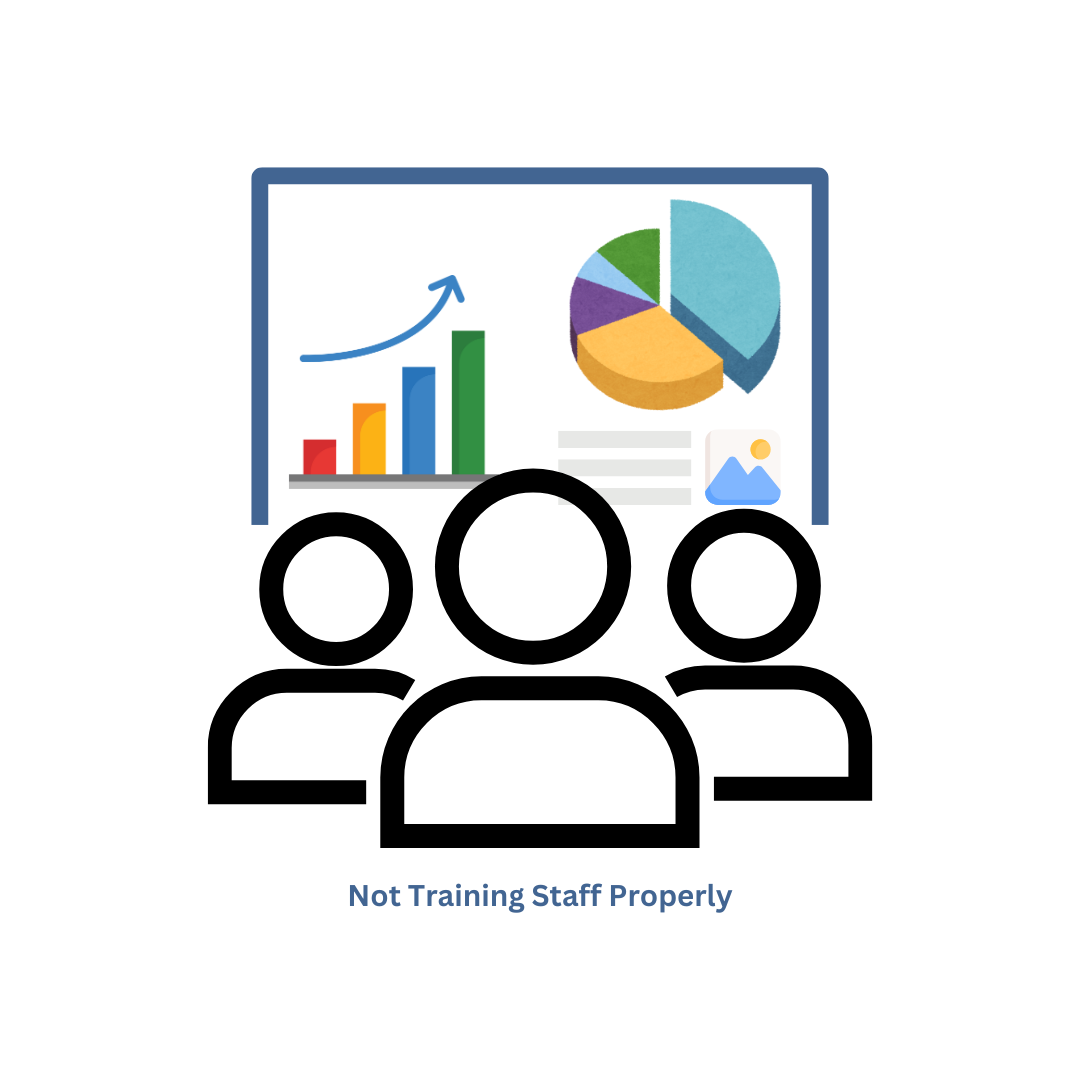
6. Not Training Staff Properly
The Mistake:
Errors will continue to happen if your staff is not properly trained in the use of your inventory management system.
How to Avoid It:
Make sure all employees get enough training on using Tracmor. Tracmor’s simple design makes learning easier for all users; however, mistake reduction needs appropriate training.
Tracmor provides a YouTube channel with useful videos on how to use the system to help your team even more. These videos are an excellent source for further learning, whether they are for configuring new features or solving common issues. To get the most of Tracmor, encourage your employees to view these tutorials.
Conclusion
Avoiding these common inventory management mistakes is crucial for running a smooth and efficient operation. With Tracmor, you can effectively control your inventory, reduce errors, and increase overall productivity. By using Tracmor’s features like real-time tracking and inventory forecasting, you’ll keep your business running smoothly and your customers satisfied.
Ready to take your inventory management to the next level? Sign up for Tracmor here or schedule a demo to see how it can work for your business.
Remember, good inventory management is the backbone of any successful business—so take the time to get it right!